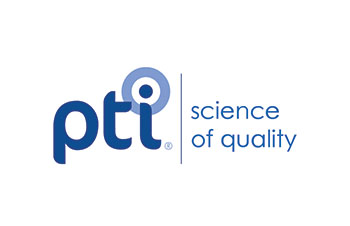
ABOUT US
PTI Inspection SystemsPTI is a global leader in package testing equipment for the medical device and pharmaceutical industries. We offer inspection systems for package leak testing, seal integrity and container closure integrity testing (CCIT). Our technologies exclude subjectivity from package testing, and use test methods that conform to ASTM standards. PTI’s inspection technologies are deterministic quantitative test methods. We specialize in testing solutions for porous and non-porous pouches, Tyvek packaging, Tyvek pouches and Tyvek lidded trays. PTI offers the entire solution including test method consulting and equipment validation.
PTI offers two non-destructive technologies to inspect medical device packaging; vacuum decay and airborne ultrasound. Both technologies aim to offer quantitative and deterministic test results to evaluate package quality. The two technologies are vastly different in function and performance. Vacuum decay is focused on package integrity and detection of leak paths. Airborne ultrasound is focused on seal inspection and seal quality. Contact us to learn more.
CONTACT INFORMATION
PTI Packaging and Inspection Systems
8 Skyline Drive
Hawthorne, NY 10532
UNITED STATES
Phone: 914.337.2005
Fax: 914-337-8519
VIDEOS
-
PTI is integrating the latest technologies for inspecting pouch seals utilizing a method that inspects and analyzes pouch seals non-destructively. Seal-Scan and Seal-Sensor utilize Airborne Ultrasonic Technology (ABUS) that inspects and analyzes pouch seals non-destructively.
-
The VeriPac FLEX Systems are available in several configurations to accommodate various package specifications. Each model achieves a specific range of test sensitivity and various test chamber sizes are available depending upon the package size and characteristics.
-
Seal Integrity Monitoring System (SIMS) 1915+, is the ideal choice for your helium based leak detection system. Using helium as the tracer gas, packages can be quantitatively tested to levels far exceeding the vacuum bubble and dye penetration test methods. This quantitative approach allows direct comparison across various packaging materials and forms, production line settings and stability storage conditions, supporting the entire lifecycle.
-
PTI-Packaging Technologies & Inspection is headquartered in Hawthorne, New York, a Westchester county community close to New York City. We are a team of engineers, scientists and professionals serving the packaging industry as a leading equipment manufacturer of package inspection equipment. PTI’s inspection technologies are deterministic test methods that produce quantitative test result data. Our technologies conform to ASTM and other regulatory standards. We specialize in offering our customers the entire solution including test method development and packaging inspection equipment validation. PTI installations have been successful in globally transferable and validated test methods.
-
PTI’s VeriPac LPX automated inline pouch inspection system assures package seal integrity of flexible packaging formats. Non-destructive vacuum decay technology and ASTM Test Method F2338 provides automated quality control using high speed robotic pick & place handling.
WEBINARS
-
在这个网络研讨会,您将了解如何评估测试我thod accuracy, information, and data analysis, how to carefully define method transfer objectives for each application, and more.
-
This video discusses the importance of protecting package contents from contaminants, including challenges associated with transport and specifically how altitude and latitude affect packaging formats.
-
This webinar takes a look at the pros and cons of manual visual inspection. Join us in taking a deeper dive into this probabilistic test method.
-
This short podcast focuses on experimental design and statistical tools we use with non-destructive package integrity test systems that produce reliable and robust quantitative test data.
CASE STUDIES
-
High product costs and superior quality requirements are the two single reasons for successful integration of airborne ultrasound seal inspection for medical device packaging. This case study focuses on the use of Seal-Scan® for final seal quality verification for an implantable sterilized medical device.
-
This study shows that HVLD can detect leaks down to the Maximum Allowable Leakage Limit (MALL) and arguably makes it one of the most sensitive leak test methods in the market.
-
The study addresses the common concern that vacuum decay is not a suitable test solution for detecting microleaks in parenteral containers if the product contains large molecule or proteinaceous liquids.
-
A nondestructive integrity-testing method will help an implant maker expand its testing program with little effort.
-
Medical device manufacturing is a labor intensive process, requiring operator involvement from manufacturing through final inspection of products. High product costs and superior quality requirements are two reasons for successful integration of airborne ultrasound seal inspection for medical device packaging.By PTI Inspection Systems
-
Ophthalmic products come in a variety of package formats. The liquid-filled packages are often soft containers with snap-on or screw caps, and include foil lidded blister packs for single-use contacts.
WHITE PAPERS
-
Experimental Design And Positive Controls For Package Integrity4/9/2020
Given that the experimental design has only two conditions, leaking and non-leaking, this variable is extremely important to understand. Proper use of positive controls and knowledge of how alternative approaches are applied to challenge a test method support the validity and reliability of the method.
-
Container Closure Integrity Testing: Sensitivity, Automation, Efficiency4/6/2020
Explore the need for sensitive, reliable, and automated container closure integrity testing technologies, and how existing deterministic solutions can help achieve optimum quality assurance goals.
-
Dye Ingress For CCIT: A Poor Bet In A High Stakes Game3/23/2020
The dye ingress test method continues to be a widely used test method for container closure integrity. This paper explains why the dye ingress test method is not a suitable approach.
-
Risk Mitigation Of Parenteral Packaging With Container Closure Integrity7/17/2019
Parenteral delivery systems are the highest risk packaging application concerning container closure integrity. Leaks that register in the single micron range can introduce a threat of bacterial ingress.
-
New Guidelines Offer Menu Of Standard Sterile Package Tests3/5/2019
High-risk packaging applications, such as pharmaceutical and class III medical devices, are coming under increasing scrutiny. A package protects the product throughout the product life cycle, and package integrity is a significant pocket of risk that can be mitigated.
-
An Introduction To Vacuum Decay Leak Testing10/9/2018
Vacuum decay is a test method provides significant savings by not wasting product for a leak test, and generates return on investment in under six months for many products.
-
Viscous Products No Match For New Container Closure Integrity Technology9/5/2018
New product types and packaging configurations, such as highly viscous formulations, pose a threat to traditional leak-testing methods, challenging current practices for container closure integrity testing.
-
Container Closure Integrity Testing Of Intravenous Bags8/21/2018
A non-invasive, non-subjective solution that is capable of detecting package leaks and invisible defects using a differential pressure transducer leak test system.
-
Understanding Ultrasound Technology To Inspect Pouch Seals
Traditional test methods of testing pouch seals are often destructive and can be unreliable. However, ultrasound technology offers a non-destructive means to ensure pouches are airtight.
-
Flexible Insights
As more and more packages and processors convert to flexible packaging from more traditional forms of rigid methods including metal cans, PET and glass bottles or jars, they are confronted with the concern and challenge of how do they insure or equal the seal integrity levels from flexible packaging that they have come to expect from these more traditional packaging methods.Submitted by PTI Inspection Systems
-
How Important Is The Physical Integrity Of The Blister Package?
Untold millions of medicinal tablets and capsules are produced every year, and many of the over-the-counter varieties are encased in blister packs for protection. Existing manual methods for inspecting these packages are subjective and lack repeatability, while electronic techniques have to date been stymied by the great variation in blister packages.
-
Pouch Seal Inspection — Airborne Ultrasound Technology For Better Process And Quality Control
A pouch seal is a structural element that joins flat film material and a component designed to close a pouch airtight. Traditional test methods (e.g. peel strength or burst), can measure the joint strength of the pouch seal using destructive methods that are often unreliable.Submitted by PTI Inspection Systems
-
Container Closure Integrity Testing For Prefilled Syringes
在本文中,我们强调我们当前的思考in an attempt to devise a systematic approach for CCI testing method selection, development, and validation.
-
Understanding Vacuum Decay Leak Testing
The ability to detect leaks is necessary to ensure consistency and integrity of packages. It is also important to detect leaks and defects that are not visibly detectable. VeriPac's non-destructive technology is capable of detecting package leaks and invisible defects using an absolute or differential pressure transducer leak test system.Submitted by PTI - Packaging Technologies & Inspection
-
Technology Overview: How To Leak Test Blister Packaging
Most current test methods for blister packages are destructive, time consuming, not sensitive, unreliable, and dependent on the properties of the package lidding material. Small semi-rigid, flexible, and multi-cavity blister packages do not have enough air inside the package to reliably detect defects by simple vacuum decay methods.Submitted by PTI - Packaging Technologies & Inspection
-
Understanding Pressure Decay Leak Testing For Bottles And Containers
Leak detection of empty containers — before the filling and sealing process — is an important step to insure container integrity. Applications in the plastic, blow molding, food, beverage and pharmaceutical industries all require some type of online container integrity system.Submitted by PTI - Packaging Technologies & Inspection
-
Blister Pack Leak Detection: Protecting Product Integrity
The blister packaging process for tablets and capsules is unique to the packaging industry in so many ways. Blister packaging will always exist due to its practicality; but, the things that make blister packaging difficult to work with also make it a desired product presentation.Submitted by PTI Inspection Systems
-
Container And Closure System Integrity Testing In Lieu Of Sterility Testing As A Component Of The Stability Protocol For Sterile Products
The purpose of stability testing is to provide evidence on how the quality of a substance or product varies with time under the influence of a variety of environmental factors such as temperature, humidity, and light, which enables you to establish or modify recommended storage conditions, retest periods, and shelf life or dating period, as the case may be.