The Market For 3D Printed Bioresorbable CMF Plates And Other Complex Devices Is Being Redefined By New GMP-Grade Filament Material
By Balaji Prabhu, Director Strategic Marketing, Medical Device Solutions, Evonik Health Care
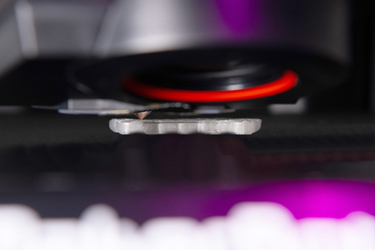
The last decade has seen 3D printing innovations redefine what’s possible across a range of industries including automotive, consumer goods, aerospace, and healthcare. However, the adoption of 3D printing technologies for implantable medical devices has been relatively slow. To a large extent, this has been due to challenges in sourcing the right biocompatible materials, the validation of processes, and adhering to quality and regulatory requirements. Where medical device innovation has occurred for 3D printing to date, it has largely been confined to metal-based implants traditionally used for hip, knee, and spine reconstruction applications.
While well-characterized bioresorbable polymers with sufficient strength and biocompatibility have now begun to replace metallic materials across traditional device applications, it has been difficult to process them into forms such as filaments and powders that are compatible with established 3D printing technologies. For example, the use of polymers such as poly(L-lactide) or poly(caprolactone) with Fused Filament Fabrication (FFF) systems has required a processing solution that can enable patient-specific geometries and a bone-like, porous structure without sacrificing essential functional properties.
One particular market gap has been cranio-maxillofacial (CMF) plates, which are used in surgeries for congenital or acquired defects of the skull and facial region. Here, it is essential that filament-based bioresorbable polymers be able to maintain mechanical properties including strength, durability, flexibility and the elimination of stress shielding during processing with FFF systems to ensure each CMF plate is printed to a sufficiently high resolution and devoid of defects.
FFF systems have long been considered an attractive opportunity to create bioresorbable CMF plates that are personalized to the individual patient. That is because they are highly efficient at the creation and consistent replication of parts with complex geometries. In particular, parts made by FFF typically have a high compressive strength in the z direction and attractive tensile properties in the xy direction. Furthermore, they are not as complex and generally cheaper to purchase and operate compared to Selective Laser Sintering (SLS) systems.
Materials utilized with FFF systems must typically be designed for the continuous feeding of a spaghetti-like filament material from a spool through a moving, heated extruder nozzle. The nozzle then prints the melted filament into a final device one layer at a time. Typically, the layer height ranges from 0.05 mm to 0.3 mm with a tolerance of +/- 0.1 mm. Until recently however, no GMP-grade polymer filament for bioresorbable devices has been available.
As one of the world’s leading suppliers of biomaterials, Evonik has recently addressed this unmet market need with its development of the RESOMER® Filament line of standard and custom bioresorbable polymers. Standard RESOMER® Filament products are provided in spools with a filament diameter of either 1.75 mm (Standard) or 2.85 mm (Customized). To address specific strength, modulus, flexibility and elongation property requirements, a range of filament grades are available with compositions including poly(L-lactide), poly(L-lactide-co-glycolide), poly(caprolactone) and polydioxanone.
As with all RESOMER® products, all filament grades undergo hydrolysis degradation in vivo, and are eliminated through excretory pathways. The degradation times of Standard RESOMER® Filament products range from less than six months to more than three years.
Many other mechanical properties can also be precisely tailored to match the requirements of the target application. Under RESOMER Filament Select®, a range of additional customized options are also available including mechanical properties, filament diameter, additives and sterilized filaments for point-of-care printing. They are also made in ISO Class 8 clean rooms, compliant with ISO 13485 and a robust global quality system.
除了RESOMER®灯丝,赢创增刊y medical device customers with RESOMER® PrintPowder for 3D printing using SLS systems. A range of granule-based RESOMER® products are also suitable for use with extrusion-based systems such as freeformers and bioplotters for the 3D printing of implants and scaffolds for tissue engineering applications.
Evonik’s highly experienced technical team is available at its Medical Device Competence Center in Birmingham, Alabama, USA to support medical device customers in the development, evaluation, and 3D printing of their applications. 3D printing services include material selection and development, prototype printing for feasibility, standardized specimen printing, and printing process development and optimization utilizing FFF or other systems. To arrange a free consultation or to request a sample, contact Evonik athealthcare@evonik.com.